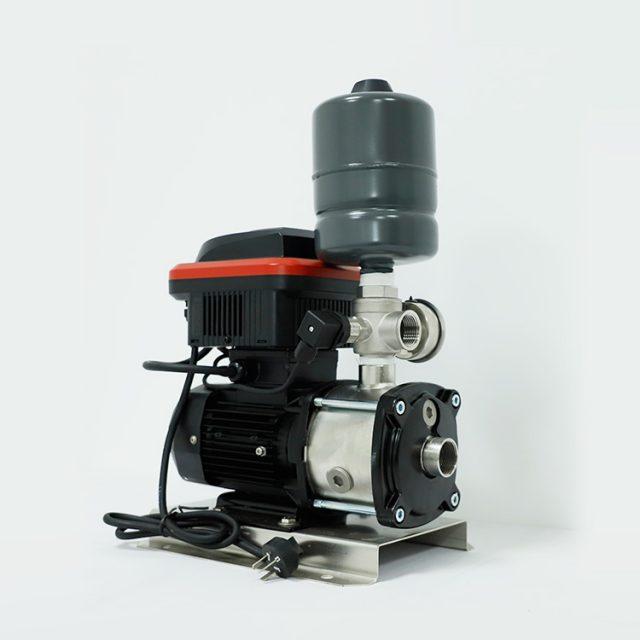
Water Pumps
A water pump is an electromechanical machine used to increase the pressure of water to move it from one point to another.
Water pumps are machines for moving water, they play a fundamental part in agriculture as they move water from its source to the fields and crops. Water pumps can be used with many forms of irrigation, such as drip, sprinklers or with a hose.
There are a wide range of water pumps available, from simple manually operated pumps to those powered by fossil fuels or electricity.
Water pumps can work in a few different ways, but in the simplest terms, water pumps consist of three main parts: an inlet, pump system and an outlet.
Water is drawn into the pump though the inlet side when a pressure difference is made within the pump system, the water wants to move from an area of high pressure to an area of low pressure. This is used to move the water through the pump to the outlet side, into a hose, and towards your farm or water tank.
Water pumps are machines for moving water, they play a fundamental part in agriculture as they move water from its source to the fields and crops. Water pumps can be used with many forms of irrigation, such as drip, sprinklers or with a hose.
It consists of two distinct parts, one is fixed to the body and the other rotates with the bearing axle. Its diameter, and the number and height of the fins, determine the flow and the pressure of the coolant in the cooling circuit. A reduction in the flow can seriously affect the life of the engine.
The main disadvantage is that they use rotation instead of suction to move water, and therefore have almost no suction power. As long as you buy a good quality pump they are generally very reliable working without attention often for years on end with complete function. They are inexpensive but an essential component in the systems that make our lives comfortable.
What do water pumps do? The main purpose of a water pumping system is to move water from one area to another. They are often applied to construction sites as a form of water extraction, assisting in the removal of water when excavating, at sewage plants, in flooded areas or when dealing with water wells and oil wells.
Submersible Pumps
A submersible pump, also called an electric submersible pump, is a pump that can be fully submerged in water.
A submersible pump (or sub pump, electric submersible pump (ESP)) is a device which has a hermetically sealed motor close-coupled to the pump body. The whole assembly is submerged in the fluid to be pumped.
Electric submersible pumps are multistage centrifugal pumps operating in a vertical position. Liquids, accelerated by the impeller, lose their kinetic energy in the diffuser, where a conversion of kinetic to pressure energy takes place. This is the main operational mechanism of radial and mixed flow pumps.
Submersible Bore Pump is also called as submergible pumps are operated particularly when it is completely submerged underwater. The mechanical seals in the motor will protect from any water entering into the pump motor and prevents short circuiting.
There are a few disadvantages with submersible pumps, and two have to do with the seal. The seals can become corroded with time. When that happens, water seeps into the motor, rendering it useless until it is repaired. Also, that seal makes the submersible pump a bit difficult to get into for repairs.
General Applications
Submersible pumps are used in these industries: drainage, slurry pumping, sewage pumping, water wells, oil wells, seawater handling, sewage treatment, fire fighting, deep well drilling, irrigation, mine dewatering, artificial lifts and offshore drilling rigs.
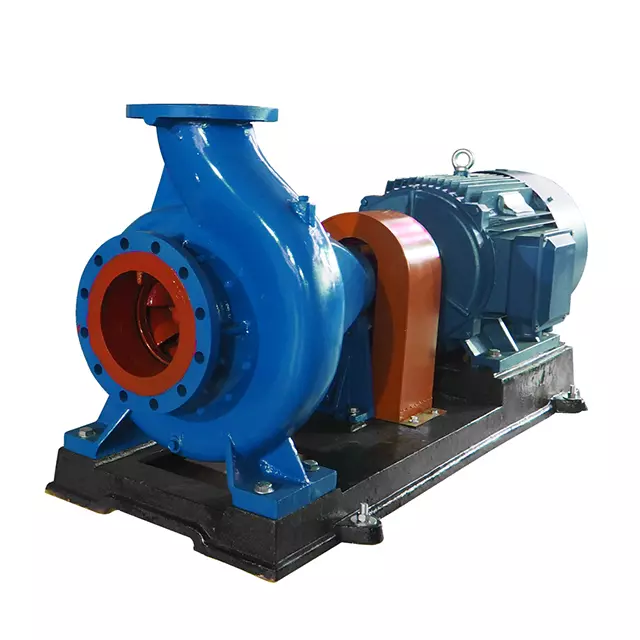
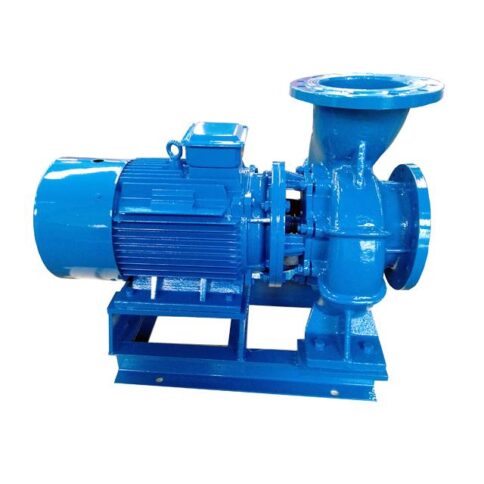
Centrifugal Pumps
Centrifugal pumps are used to transport fluids by the conversion of rotational kinetic energy to the hydrodynamic energy of the fluid flow.
A centrifugal pump is a mechanical device designed to move a fluid by means of the transfer of rotational energy from one or more driven rotors, called impellers. Fluid enters the rapidly rotating impeller along its axis and is cast out by centrifugal force along its circumference through the impeller’s vane tips. The action of the impeller increases the fluid’s velocity and pressure and also directs it towards the pump outlet. The pump casing is specially designed to constrict the fluid from the pump inlet, direct it into the impeller and then slow and control the fluid before discharge.
The impeller is the key component of a centrifugal pump. It consists of a series of curved vanes. These are normally sandwiched between two discs (an enclosed impeller). For fluids with entrained solids, an open or semi-open impeller (backed by a single disc) is preferred (Figure 1).
Fluid enters the impeller at its axis (the ‘eye’) and exits along the circumference between the vanes. The impeller, on the opposite side to the eye, is connected through a drive shaft to a motor and rotated at high speed (typically 500-5000rpm). The rotational motion of the impeller accelerates the fluid out through the impeller vanes into the pump casing.
There are two main families of pumps: centrifugal and positive displacement pumps. In comparison to the latter, centrifugal pumps are usually specified for higher flows and for pumping lower viscosity liquids, down to 0.1 cP. In some chemical plants, 90% of the pumps in use will be centrifugal pumps. However, there are a number of applications for which positive displacement pumps are preferred.
The efficient operation of a centrifugal pump relies on the constant, high speed rotation of its impeller. With high viscosity feeds, centrifugal pumps become increasingly inefficient: there is greater resistance and a higher pressure is needed to maintain a specific flow rate. In general, centrifugal pumps are therefore suited to low pressure, high capacity, pumping applications of liquids with viscosities between 0.1 and 200 cP.
Slurries such as mud, or high viscosity oils can cause excessive wear and overheating leading to damage and premature failures. Positive displacement pumps often operate at considerably lower speeds and are less prone to these problems. Any pumped medium that is sensitive to shearing (the separation of emulsions, slurries or biological liquids) can also be damaged by the high speed of a centrifugal pump’s impeller.
Centrifugal pumps are commonly used for pumping water, solvents, organics, oils, acids, bases and any ‘thin’ liquids in both industrial, agricultural and domestic applications. In fact, there is a design of centrifugal pump suitable for virtually any application involving low viscosity fluids.
A centrifugal pump operates through the transfer of rotational energy from one or more driven rotors, called impellers. The action of the impeller increases the fluid’s velocity and pressure and directs it towards the pump outlet. with its simple design, this pump is easy to operate & maintain.
Centrifugal pump designs offer simple and low cost solutions to most low pressure, high capacity pumping applications involving low viscosity fluids such as water, solvents, chemicals and light oils. Typical applications involve water supply and circulation, irrigation, and the transfer of chemicals in petrochemical plants. Displacement pumps are preferred for applications involving highly viscous fluids such as thick oils and slurries, especially at high pressures, for complex feeds such as emulsions, foodstuffs or biological fluids, and when accurate dosing is required.
Pool Pumps
Pool pumps work by drawing water from the pool, passing it through a filter to remove debris and contaminants, and then returning the clean water back into the pool. They play a crucial role in maintaining proper water circulation, preventing stagnation, and ensuring effective filtration.
The recommended runtime for pool pumps is typically around 8 to 12 hours per day, depending on factors such as pool size, bather load, and climate. It is best to consult with a pool professional to determine the optimal runtime for your specific pool.
The lifespan of a pool pump can vary depending on factors such as usage, maintenance, and quality of the pump. On average, a well-maintained pool pump can last between 8 to 12 years. Regular maintenance and timely repairs can help extend the lifespan of your pool pump.
Determining the right pump size depends on factors such as pool volume, plumbing configuration, and desired turnover rate. It is recommended to consult with a pool professional who can assess your specific requirements and recommend the appropriate pump size for your pool.
Noises from a pool pump can be indicative of various issues, such as a clogged impeller, loose components, or motor problems. It is best to have a qualified technician inspect and diagnose the source of the noise to address the problem effectively.
Pool Pump Consultation
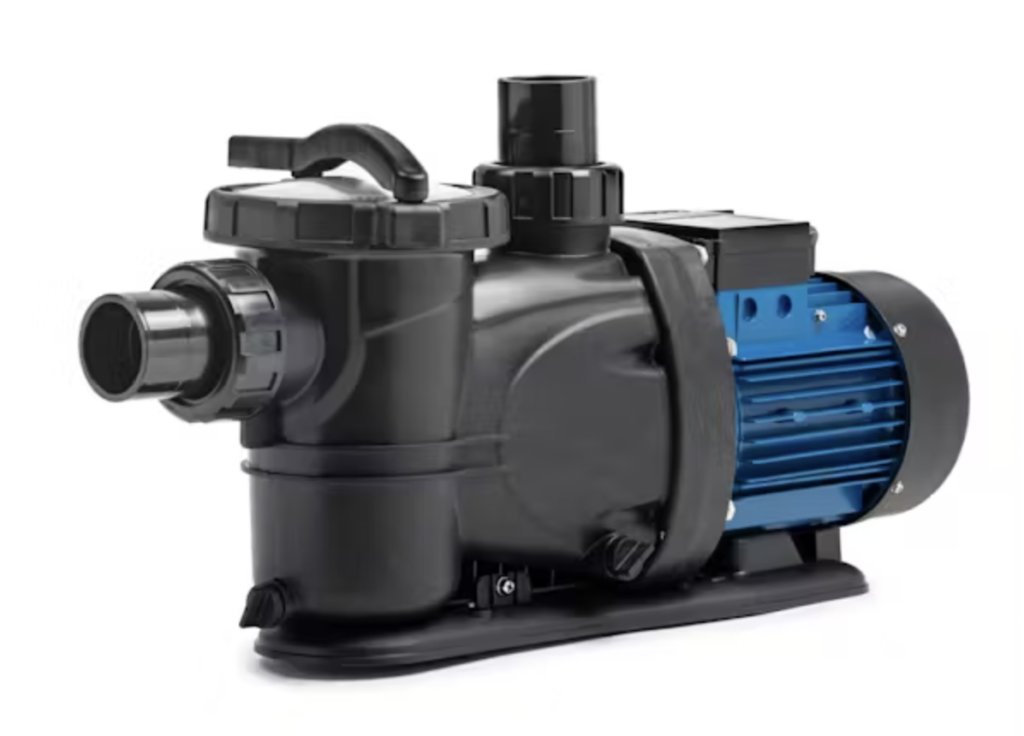
Contact Us
Contact Specialized Pumps Limited today to schedule a repair, service or to learn more about our comprehensive range of pump solutions.